Understanding Injection Mold Manufacturing: A Comprehensive Guide
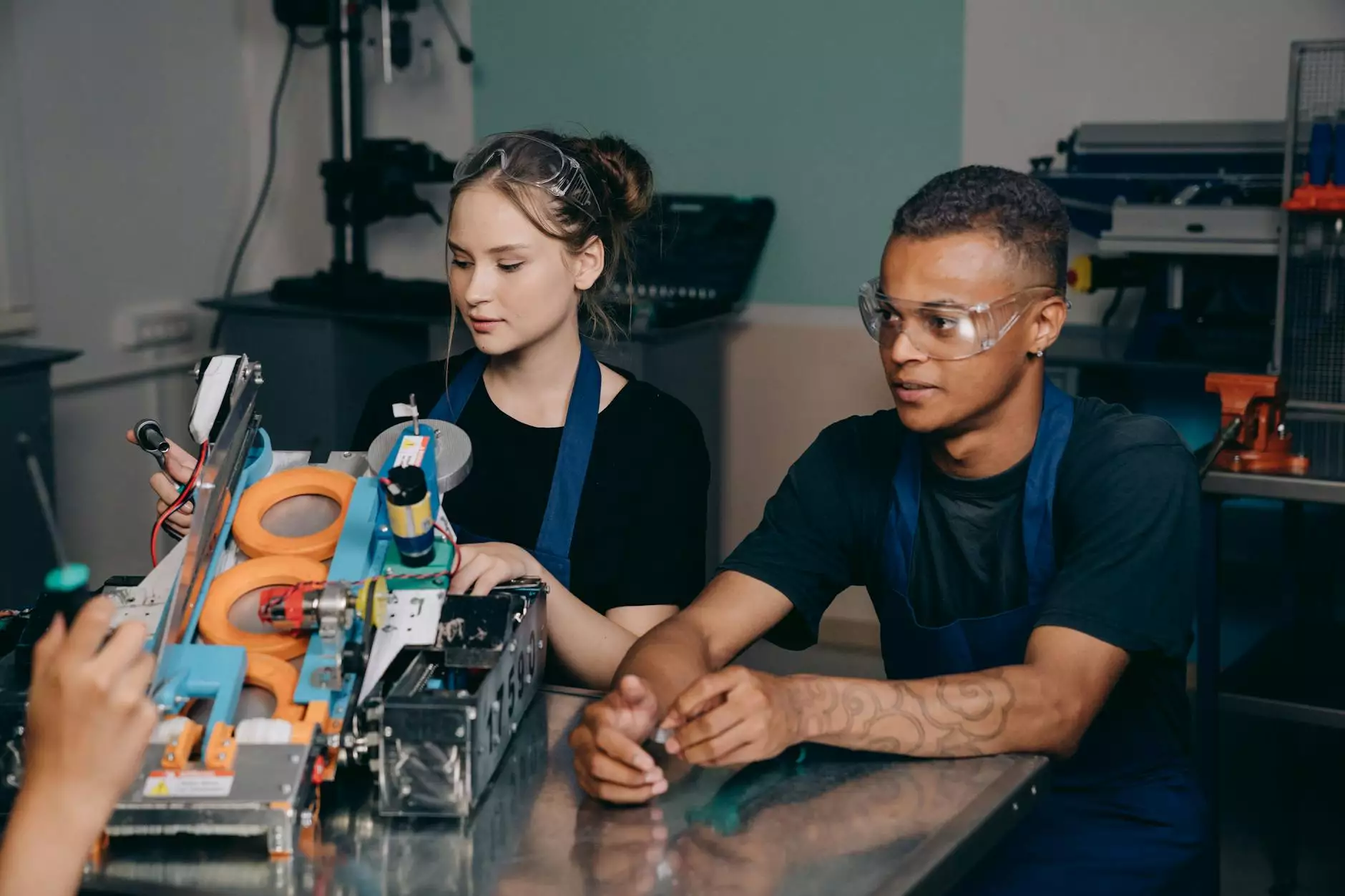
Injection mold manufacturing is a critical component of modern production processes, used widely across various industries. This article delves deep into the fundamentals of this method, examining its benefits, applications, and the technologies involved. Let’s explore the world of injection mold manufacturing and understand why it is indispensable in today’s manufacturing landscape.
What is Injection Mold Manufacturing?
Injection mold manufacturing is a process where molten material is injected into a mold cavity to create parts and products. The materials typically used include thermoplastics, thermosetting polymers, and metals. This method is renowned for its efficiency, precision, and ability to produce complex shapes at scale.
How Injection Molding Works
The injection molding process consists of several key steps:
- Material Selection: Choosing the right material based on the required properties of the final product.
- Mold Design: Creating a mold that reflects the product design, often using CAD software.
- Injection Phase: Heating the material until it is molten, then injecting it into the mold under high pressure.
- Cooling Phase: Allowing the injected material to cool and solidify in the mold.
- Mold Opening: Once cooled, the mold is opened, and the finished product is ejected.
- Finishing: Conducting any necessary post-processing, such as trimming or painting the products.
The Advantages of Injection Mold Manufacturing
Why do manufacturers prefer injection mold manufacturing? Here are several compelling reasons:
- High Efficiency: Once the mold is created, the production process can be very fast, with cycle times often less than a minute.
- Consistency and Precision: Injection molding allows for tight tolerances and complex geometries, ensuring uniformity across all units produced.
- Reduced Waste: The precision of the process minimizes excess material, making it more environmentally friendly.
- Versatility: A wide range of materials can be used, and it can produce products tailored for specific applications.
- Cost-Effectiveness: While the initial cost of mold creation is high, the per-unit cost decreases significantly as production volume increases.
Applications of Injection Mold Manufacturing
Injection mold manufacturing is utilized across various sectors, including:
1. Automotive Industry
Injection molding plays a vital role in the automotive sector, enabling the production of intricate parts such as dashboards, bumpers, and housings.
2. Consumer Goods
From toys to kitchenware, injection mold manufacturing produces countless consumer products that are functional and aesthetically pleasing.
3. Medical Devices
The medical field relies heavily on injection molding to create precise, sterile components, including syringes, valves, and surgical instruments.
4. Electronics
In electronics, it is used to manufacture casings, connectors, and other components that require durability and precision.
5. Industrial Applications
Many industrial tools and components, such as gears and enclosures, are produced using injection mold manufacturing for their robustness and reliability.
Technological Innovations in Injection Mold Manufacturing
As technology evolves, so does the injection mold manufacturing process. Some of the recent advancements include:
- 3D Printing: Rapid prototyping using 3D printing technologies allows for the quick generation of mold designs, reducing lead times.
- Advanced Materials: The development of new materials offers enhanced mechanical properties, expanding the possibilities for product development.
- Smart Manufacturing: IoT integration enables real-time monitoring and predictive maintenance of injection molding machines, improving overall efficiency.
- Micro-Molding: This technique allows for the production of tiny parts with extreme precision, beneficial for sectors like electronics and medical devices.
Challenges in Injection Mold Manufacturing
Despite its advantages, injection mold manufacturing does face certain challenges:
- High Initial Costs: The design and production of molds can be expensive, particularly for small volume runs.
- Complex Design Limitations: While injection molding can produce intricate shapes, there are still limitations based on the mold design.
- Material Limitations: Certain advanced materials may not be suitable for injection molding due to viscosity issues.
How to Choose an Injection Mold Manufacturer
Selecting the right partner for injection mold manufacturing is crucial for success. Here are some factors to consider:
1. Experience and Expertise
Choose a manufacturer with a proven track record and expertise in your specific industry.
2. Technology and Equipment
Ensure they have modern, well-maintained equipment capable of producing high-quality molds and parts.
3. Material Options
A good manufacturer should offer a variety of material options to meet your production needs.
4. Quality Assurance Processes
Look for manufacturers that employ rigorous quality control measures to ensure consistency and quality in production.
5. Customer Service
Excellent customer support can help resolve issues quickly and efficiently, making a significant difference in the manufacturing process.
Conclusion
In summary, injection mold manufacturing is a powerful manufacturing technology that offers numerous benefits across various industries. By understanding its processes, advantages, applications, and recent advancements, businesses can leverage this technology to enhance their production capabilities and product offerings. With careful selection of manufacturing partners and understanding the market’s demands, companies can thrive in an increasingly competitive landscape.
For more information on high-quality injection mold manufacturing, visit DeepMould today!