Understanding the Importance of a CNC Machining Factory in Modern Manufacturing
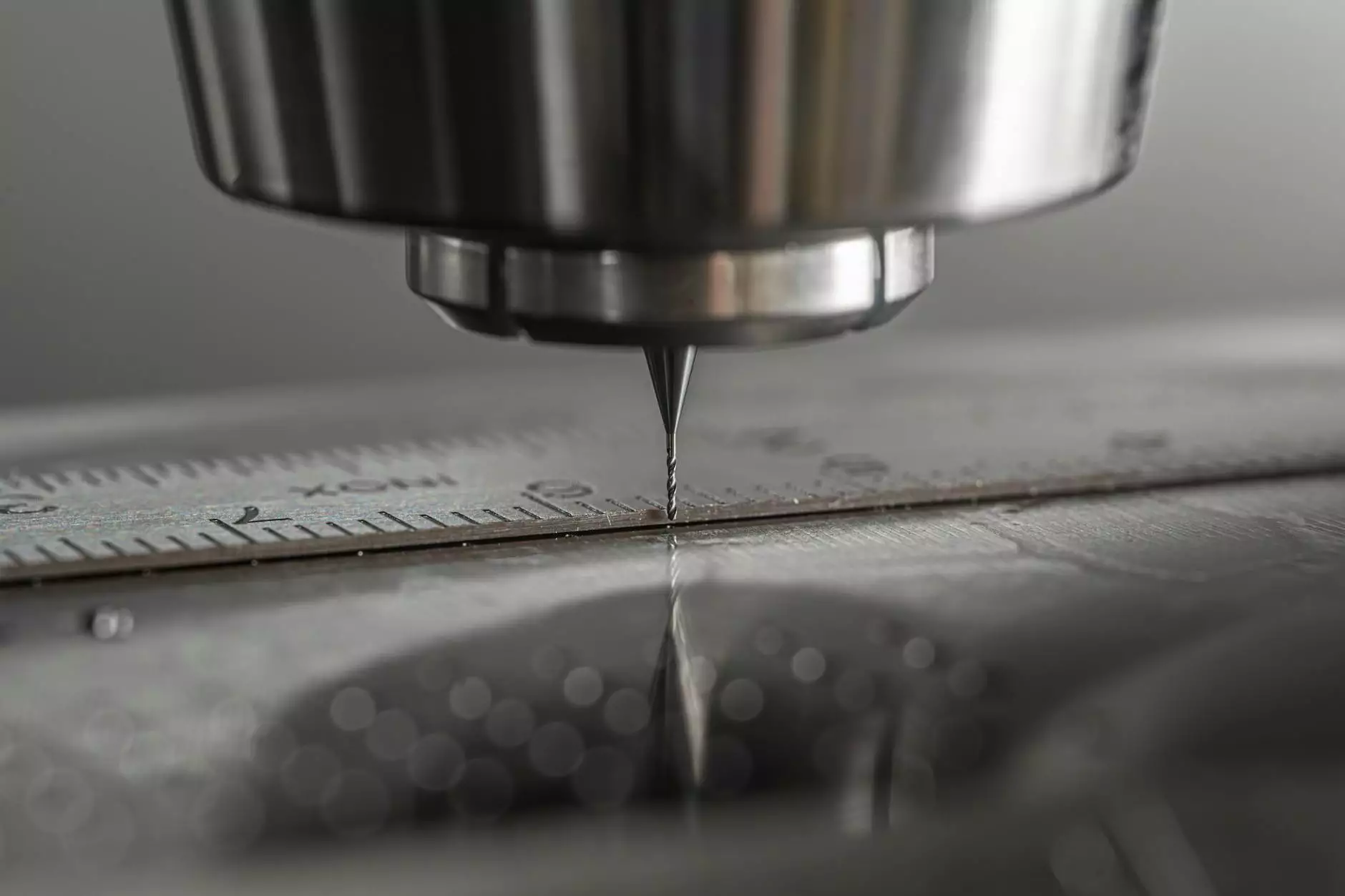
The manufacturing industry has undergone a significant transformation over the past few decades. One of the most notable advancements is the rise of the cnc machining factory, which plays a crucial role in metal fabrication and production efficiency. This article delves into the intricacies of CNC (Computer Numerical Control) machining, examining its benefits, applications, and how it has reshaped the landscape of manufacturing.
What is CNC Machining?
CNC machining is a manufacturing process that uses computerized controls to operate mechanical tools such as lathes, mills, and routers. The process is capable of producing parts with high precision, making it essential for industries that require accuracy and consistency. The key elements of CNC machining include:
- Computer Automation: Machinery is controlled by software, reducing the risk of human error.
- Precision and Accuracy: Parts can be manufactured within microns of tolerance.
- Material Versatility: CNC machines can work with a wide array of materials, including metals, plastics, and composites.
The Rise of CNC Machining Factories
The emergence of CNC machining factories has revolutionized how products are designed and manufactured. Traditionally, machining was a manual and labor-intensive process, but advancements in technology have redefined efficiencies in production. Key factors contributing to the rise include:
- Increased Demand for Customization: Clients often require unique specifications for their products.
- Globalization: The need to compete in a worldwide market necessitates efficient manufacturing solutions.
- Technological Advancements: Innovations in software and machinery enhance capabilities.
Benefits of a CNC Machining Factory
Utilizing a cnc machining factory offers numerous benefits that contribute to the overall productivity and quality of manufacturing processes. Here are some core advantages:
1. Enhanced Precision
CNC machining significantly improves the precision of components, allowing for intricate designs and complex geometries to be manufactured consistently. This is critical for industries such as aerospace, automotive, and medical devices, where even the smallest deviation can lead to catastrophic failures.
2. Increased Efficiency
With CNC machining, production processes can be automated, thus minimizing manual intervention. This leads to:
- Faster production rates
- Reduced operational costs
- Less material wastage
3. Flexibility in Production
Manufacturers can switch between different products using the same machinery with minimal downtime. This adaptability allows companies to respond to market demands swiftly, ensuring that they remain competitive.
4. Quality Control
The use of CNC machining inherently includes quality control measures as the computer software monitors every aspect of the production process, ensuring consistency and adherence to specifications. This reduces defects and rework, leading to overall cost savings.
Applications of CNC Machining
The versatility of CNC machining factories enables application across various industries. Some of the notable applications include:
- Aerospace Industry: Critical components such as engine parts and airframes.
- Automotive Manufacturing: Precision parts for vehicles like brackets, mounts, and chassis components.
- Medical Sector: Manufacturing surgical instruments and implants with high precision.
- Electronics: Creating custom housings and structures for electronic devices.
The Future of CNC Machining Factories
The future of cnc machining factories looks promising, with continuous advancements in technology paving the way for even more innovations. Emerging trends include:
1. Integration of AI and Machine Learning
Artificial intelligence is expected to enhance CNC machining processes by predicting maintenance needs, improving efficiency, and analyzing production data for better decision-making.
2. 3D Printing and CNC Collaboration
The convergence of CNC machining and additive manufacturing will lead to new possibilities in creating complex parts that combine the strengths of both technologies.
3. Sustainable Practices
With growing environmental concerns, CNC machining factories are exploring sustainable practices, such as reducing energy consumption and recycling materials.
Key Considerations for Choosing a CNC Machining Factory
When selecting a cnc machining factory for your manufacturing needs, there are several factors you should consider:
- Expertise and Experience: Evaluate the factory's background in producing parts similar to your requirements.
- Technology and Equipment: Ensure that they utilize the latest machinery and software for optimal results.
- Quality Assurance: Look for certifications such as ISO 9001 that ensure quality management standards are met.
- Customer Service: A responsive design team can greatly affect project timelines and outcomes.
Conclusion: Embracing the Future of Manufacturing with CNC Machining Factories
The role of cnc machining factories in the manufacturing landscape is undeniable. As we continue to embrace technological advancements, these factories will remain at the forefront, delivering precision, efficiency, and innovative solutions to a variety of industries. The synergy of improved production techniques, coupled with the demand for high-quality components, positions CNC machining as a critical component of future manufacturing strategies.
By leveraging the capabilities of a leading CNC machining factory like Deep Mould, businesses can achieve their production goals and maintain a competitive edge in an ever-evolving market. The future is bright for CNC machining, and its impact on manufacturing will only continue to grow.